Chapter 4
The Manufacture of Compost by the Indore Method
The aim of the Indore method of manufacturing compost is by means of a simple process to unite the advantages of three very different things: (1) the results of scientific research on the transformation of plant residues; (2) the agricultural experience of the past, and (3) the ideal line of advance in the soil management of the future -- in such a manner that all the by-products of agriculture can be systematically converted into humus. An essential feature of this synthesis is the avoidance of anything in the nature of fragmentation of the factors. All available vegetable matter, including the soiled bedding from the cattle-shed, all unconsumed crop residues, fallen leaves and other forest wastes, farmyard manure, green-manures and weeds pass systematically through the compost factory, which also utilizes the urine earth from the floor of the cattle-shed together with the available supply of wood ashes from the blacksmith's shop and the workmen's quarters. The only other materials employed are air and water. This manufacture is continuous right through the year, including the rainy season, when a slight modification has to be made to ensure sufficient aeration. The product is a finely divided leaf-mould, of high nitrifying power, ready for immediate use. The fine state of division enables the compost to be rapidly incorporated and to exert its maximum influence on a very large area of the internal surface of the soil.
The Indore process thus utilizes all the by-products of agriculture and produces an essential manure. Besides doing this any successful system of manufacturing compost must also fulfil the following conditions:
- The labour required must be reduced to a minimum. The process must fit in with the care of the work cattle and with the ordinary working of the farm.
- A suitable and also a regular carbon-nitrogen ratio must be produced by well mixing the vegetable residues before going into the compost pits. Unless this is arranged for, decay is always retarded. The mixing of these residues, combined with the proper breaking up of all refractory materials is essential for rapid and vigorous fermentation and for uniformity throughout the process.
- The process must be rapid. To achieve this it must be aerobic throughout, and must include arrangements for an adequate supply of water and for inoculation, at the right moment, with the proper fungi and bacteria. The general reaction of the mass must be maintained, within the optimum range, by means of earth and wood ashes. The maintenance of the proper relationship between air and water, so that no delay takes place in the manufacture, proved to be the greatest practical difficulty when evolving the process.
- There should be no losses of nitrogen at any stage; if possible, matters should be so arranged that fixation takes place in the compost factory itself and afterwards in the field. To conserve the nitrogen, the manufacture must stop as soon as the compost reaches the nitrification stage, when it must either be used or banked. It can best be used as a top dressing for irrigated crops; it can be preserved, as money is kept in a bank, by applying it to the fields when dilution with the large volume of soil arrests further changes till the next rains.
- There must be no serious competition between the last stages of the decay of the compost and the work of the soil in growing a crop. This is accomplished by carrying the manufacture of humus up to the point when nitrification is about to begin. In this way the Chinese principle of dividing the growing of a crop into two separate processes -- (1) the preparation of the food materials outside the field, and (2) the actual growing of the crop -- can be introduced into general agricultural practice.
- The compost should not only add to the store of organic matter and provide combined nitrogen for the soil solution but should also stimulate the micro-organisms.
- The manufacture must be a cleanly and a sanitary process from the point of view both of man and also of his crops. There must be no smell at any stage, flies must not breed in the compost pits or in the earth under the work cattle. The seeds of weeds, the spores of harmful fungi, the eggs of noxious insects must first be destroyed and then utilized as raw material for more compost. All this is achieved by the combination, in the compost pits during long periods, of high temperature and high humidity with adequate aeration.
The Compost Factory
The compost factory at Indore adjoins the cattle shed. This latter (Plate III) has been constructed for forty oxen and is provided with a cubicle, in which a supply of powdered urine earth can conveniently be stored. The cattle stand on earth. A paved floor is undesirable as the animals rest better, are more comfortable and are warmer on an earthen floor. The earth on which the cattle stand absorbs the urine, and is replaced by new earth to a depth of six inches every three or four months.
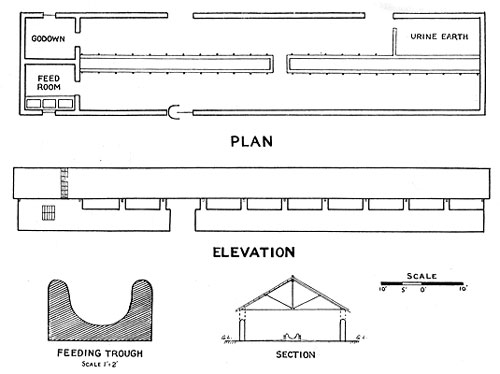
Plate III. Cattle-shed.
|
The compost factory (Plates IV) itself is a very simple arrangement. It consists of thirty-three pits, each 30 ft. by 14 ft. and 2 ft. deep with sloping sides, arranged in three rows with aufficient space between the lines of pits for the easy passage of loaded carts. The pits themselves are in pairs, with a space 12 ft. wide between each pair. This arrangement enables carts to be brought up to any particular pit. Ample access from the compost factory to the main roads is also necessary, so that during the carting of the compost to the fields, loaded and empty carts can easily pass one another, and also leave room for the standing carts which are being filled. For a large factory it is an advantage to have water laid on, so that the periodical moistening of the compost can be done by means of a hose pipe. At Indore, water is pumped through a 3 in. pipe into a pressed steel tank, 8 ft. by 8 ft. by 8 ft., holding 3,200 gallons, which is carried on walls, 4 ft. above the ground, to provide the necessary head. This supply lasts about a week. Water is led by 1-1/2 in. pipes from the tank to eight taps, to which the armoured hose can be screwed. Each tap serves about six pits. The general arrangement will be clear from Plate IV.
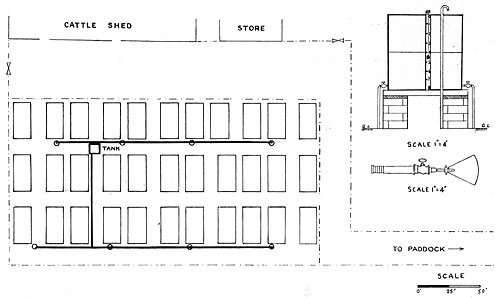
Plate IV. Plan of compost factory at Indore.
|
The total cost of the water tank, including arrangements for distribution, was Rs. 1650 (equivalent to about 120 pounds sterling). This was made up as follows: tank, Rs. 750; pipe system, Rs. 466; girders for tank, Rs. 31; armoured hose, Rs. 28: railway freight, Rs. 88; masonry work, Rs. 148; labour, including fitting up, Rs. 129.
The space under the tank, which is walled in on three sides and is open on the leeward side, is used for storing wood ashes, and for keeping the tubs and implements needed for the making of compost.
For a smaller factory or for the small holder, such a water system is not necessary. All that is needed is that the compost pits should be arranged near a well.
Collection and Storage of the Raw Material
Plant Residues
All vegetable wastes from the cultivated area -- such as weeds, cotton and other stalks, green-manure, cane-trash, fallen leaves and so forth, and all inedible crop residues from the threshing floor -- are carefully collected. All woody materials like cotton and pigeon-pea (Cajanus Indicus Spreng.) stalks are crushed by placing on the farm roads to be trampled and reduced by the traffic to a condition resembling broken up wheat straw (Plate V). All green materials -- such as weeds and green-manures -- are withered for at least two days before use or storage. All these various residues are stacked near the cattleshed as received, layer by layer -- if possible under cover during the rains -- so that these materials may become thoroughly mixed. Each layer must not be more than one foot thick, otherwise difficulties arise in making a suitable mixture. Care must also be taken to remove the stacked material in vertical slices so as to ensure even mixture. Very hard and woody materials -- such as sugarcane and millet stumps, wood shavings, sawdust and waste paper -- should be dumped separately in one of the empty compost pits with a little earth and kept moist. After this preliminary treatment, these hard and resistant materials can be readily composted. Steeping such materials in water for two days, before addition to the bedding under the work cattle, serves the same purpose.
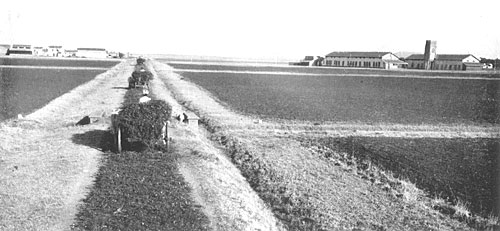
Plate V. Crushing cotton salks by road traffic.
|
Urine Earth and Wood Ashes
All the earth removed from the silage pits, all earthy sweepings from the threshing floors and all silt from drains are stored in a convenient place near the cattle-shed. This provides an adequate supply of suitable earth for absorbing the urine of the work cattle, and acting as a base in the making of compost. This earth is spread evenly on the cattle-shed floor to a depth of six inches and renewed every three or four months. Half the urine earth when removed from the floor should be crushed (Plate VI) in a mortar mill(See Plate's V and VI). to break up the large lumps, and should be stored under cover as dry powdered urine earth. The other half of the urine earth should be applied direct to the fields as manure. All available wood ashes should be stored under cover, as in the case of the powdered urine earth. These materials (urine earth and wood ashes) are as essential in the manufacture of compost as the plant residues themselves.
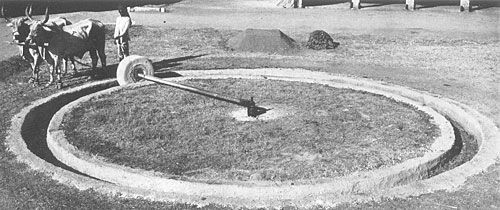
Plate VI. Powdering urine earth in a mortar mill.
|
Water and Air
Both water and air are needed for the compost process, which therefore must be carried out near a well or other source of fresh water.
Arrangement and Disposal of the Bedding under the Work Cattle
(All quantities in the following refer to one pair of oxen. The figures should be multiplied, when necessary, by the number of pairs of oxen kept.)
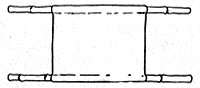
Fig. 1. A stretcher (pal) for removing bedding.
|
All the uneaten food and any damaged silage are thrown on the wet portions of the cattle-shed floor. One and a half pals (Fig. 1) of stacked vegetable refuse, together with not more than one-twentieth of this amount of hard resistant material (such as wood shavings, sawdust or waste paper) from the soaking pit are spread on the floor. (A pal is a stretcher made of a piece of gunny sheet, 4 ft. by 3 ft., nailed to two bamboos each 7 ft. 6 in. long.) The cattle sleep on this bedding during the night. In this way the bedding gets crushed and broken still further and also impregnated with urine. Next morning one-fourth of a tagari (Fig. 2) of fresh dung is removed to the compost pit; the rest of the cattle dung being scattered on the bedding in lumps not bigger than a small orange; or this excess dung can be made into cow-dung cakes (kundas) for fuel.
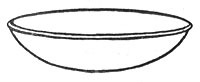
Fig. 2. A sheet-iron bowl (tagari).
|
(A tagari is a bowl made of sheet iron, capacity five-sevenths of a cubic foot. In Table IV the metal bowls are converted into pounds or double handfulls of the materials used. Kundas, thin flat cow-dung cakes, about twelve inches in diameter and one inch thick, are used in the villages of India as fuel for the cooking of food.) Two-fifths of a tagari of dry urine earth is sprinkled on the used bedding in the same manner as murum (Murum is the Hindustani name of the permeable layer of decayed basalt which underlies the black cotton soils of India) is spread on roads.
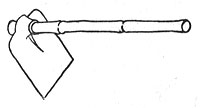
Fig. 3. A spade (phawra) used in compost making.
|
The bedding is then transferred by a spade (Fig. 3) on to the pal from one end to the other and removed to the compost pit. In this way the raw material used for the compost is made perfectly homogeneous. The earthen floor of the cattle-shed should then be swept clean, the sweepings being removed on a pal to the compost pit. All wet patches on the floor are covered with new earth, after scraping out the very wet portions. In this way all smell in the cattle-shed is avoided and the breeding of flies in the earth underneath the animals is entirely prevented. Bedding for the next day can then be laid as described above.
During the rains, the bedding should consist of three layers -- a bottom layer and a top layer of dry material specially reserved for the purpose, any withered residues being sandwiched in between. On very wet days, all the urine earth may be added to the bedding before removal to the compost heap.
The volume and weight of the various materials which are moved to and fro in the sheet-iron bowls (tagaries) are given in Table IV.
Table IV
Volume (In Double Handfulls) and Weight (In Lb.) of the Contents of a Tagari
|
|
Volume in double handfulls
|
Weight in lb.
|
Fresh dung |
6.5
|
39.5
|
Powdered urine earth |
20.5
|
22.5
|
Wood ashes |
15
|
20
|
Fungus innoculant |
5
|
20
|
Bacterial innoculant |
6
|
20
|
Refractory vegetable residues |
6
|
9
|
Mixed vegetable residues |
|
9
|
Impregnated bedding |
|
16.5
|
Sweepings from the cattle-shed floor |
|
19
|
Charging the Compost Pits
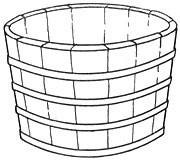
Fig. 5. A wooden tub for slurry.
|
A convenient size for a compost pit is 30 ft. by 14 ft. and 2 ft. deep with sloping sides. The depth of the compost pit is most important on account of the aeration factor. It should never exceed 24 in. A wooden tub (Fig. 4), a rake (Fig. 5), a bowl (tagari) (Fig. 2), and a few empty kerosine tins (each holding four gallons) with handles (Fig. 6) are all that are needed besides the pal (Fig. 1).
The following materials are placed alongside each compost pit -- powdered urine earth, two-fifths tagari, fresh dung, one-quarter tagari; fungus material, three-tenths tagari, taken from a compost pit ten to fifteen days old; wood ashes, one twentieth tagari; water, one kerosine tin. The wood ashes and one-twentieth of a tagari of urine earth are mixed with some dung and fungus material in a portion of the water to make a thin slurry. The pals of bedding should be added, as they arrive, from one edge of the pit by simply allowing the bamboo pole of the pal next the pit to fall into it (Plate VII).
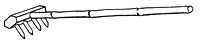
Fig. 5. Wooden rake for charging pits.
|
The other pole is then lifted so that the rest of the bedding drops easily into the pit. The material is then spread by means of the rake in a layer, not exceeding two inches thick over the compost pit. All trampling of the charged pit must be avoided as this interferes with aeration. Some dry urine earth and then the stirred slurry are first sprinkled thinly on each charge of bedding, which should appear evenly wetted. The soaked residues from the tub are then scattered on each layer of bedding.
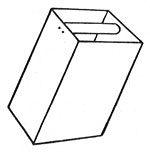
Fig. 6. Water tin.
|
This inoculates the mass with active fungus throughout. The polished surfaces of the bedding are also covered with an active adherent coating. This leads to rapid and even crumbling. The volume of the slurry is made up with more dung, fungus starter and water as required. The pit is charged with the bedding, layer by layer, until all the bedding is used up. The sweepings from the cattle-shed floor, which are rich in urine, are sprinkled on the top of each day's charge with a tagari, followed by one-third of a tin of fresh water. This distributes the urine evenly throughout the daily charge and also prevents excess drying. Another watering in the evening, with two-thirds of a tin, and a third watering the next morning with one-third of a tin completes the charge. The pit or a suitable portion of it should be filled up to the brim in six days or less, the remaining part being filled subsequently. (The period of charging must not exceed six days, whether or no the pit is completely filled by then. Each six days' charge should be regarded as one unit in the manufacture of compost, no matter whether the pit is filled completely or not.) Everything is now ready for the development of an active fungus growth (the first stage in the manufacture of compost). When properly managed, a vertical section of the fermenting mass should appear quite uniform and should not show any alternate layers.
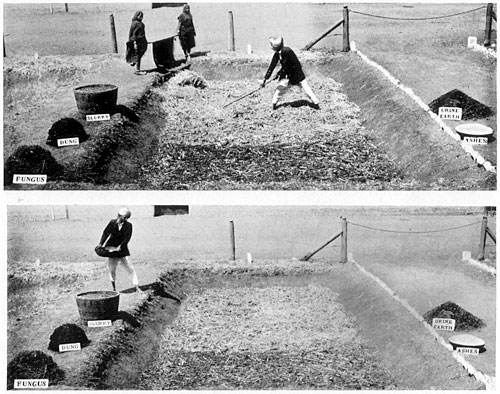
Plate VII. Charging the Compost pits: (1) Charging the Compost pits; (2) Applying the slurry
|
As the pits are frequently full of water during the greater part of the rains, the compost must be made in heaps (Plate VIII) from the middle of June to 1 October. The dimensions of the heaps should not exceed 7 ft. by 7 ft. at the top, 8 ft. by 8 ft. at the bottom and 2 ft. in height. The dimensions of these monsoon heaps (any one of which is not necessarily completed by the amount of vegetable waste which can be accumulated in six days) must not be exceeded, otherwise aeration difficulties are certain to be encountered. The decomposition in heaps during the rains does not take place so evenly as in the pits.
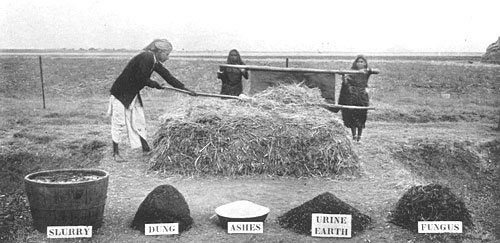
Plate VIII. Compost manufacture in the rainy season
|
During the early rains, all the material in the pits must be transferred to heaps on the surface. This is most conveniently done at the time of the first, second or third turn.
The subsequent waterings are most important, otherwise decay will stop. The first watering is done twelve days (days should be counted from the date on which the filling of the pit begins) after charging, when 1.25 tins are added evenly over the whole surface. Further water is added at the time of the first, second and third turning and afterwards as needed. During the rains, the quantity of water as given above must be added at the time of charging; the subsequent waterings during the rains may be reduced or completely omitted according to the weather. Stagnant rain-water from the pits should never be used. When watering is done by a hose pipe from a tank as at Indore, the amount added can easily be adjusted if the rate of flow is known.
Turning the Compost
To ensure uniform mixture and decay, and to provide the necessary amount of water and air as well as a supply of suitable bacteria, it is necessary to turn the material three times. The only difficulty which is likely to arise in the process is the establishment of anaerobic conditions between the period of charging and the first turn. This can be caused by overwatering or by want of attention to the mixing. It is at once indicated by the smell and by the appearance of flies attempting to breed in the mass. When this occurs, the heap should be turned at once with the addition of dung slurry and wood ashes.
First turn.
Sixteen days after charge (Plate IX). Sufficient fresh water should be ready -- about four tins according to the season. Three-fifths of a tagari of compost is taken from another pit thirty days old (just after the second turn) and scattered on the surface of the material. This is necessary for inoculating the mass with the proper bacteria. The top layer of the compost is then loosened and mixed, a portion at a time, with a rake and well moistened with water. Half the heap is sliced with a spade a few inches breadthwise and vertically from top to bottom to fill one tagari at a time. Tagari after tagari is poured in rows on the other undisturbed half to make a layer which is then sprinkled with water. This is repeated until one-half of the contents of the pit is doubled lengthwise over the other. The heap is then watered, suflicient being added at this first turn to prevent the wasteful use of water afterwards. After turning, the heap should not rise more than twelve inches above ground level. The second watering, 1.5 tins, is given twenty-four days after charge. At the first turn, the materials should be arranged on the windward side of the pit to avoid the cooling of the mass and also excessive drying. During the rains, when heaps are made, it is not possible to double one-half of the heap over the other. The material should then be completely turned and the heap re-made. The heaps should be made as near as possible to each other.
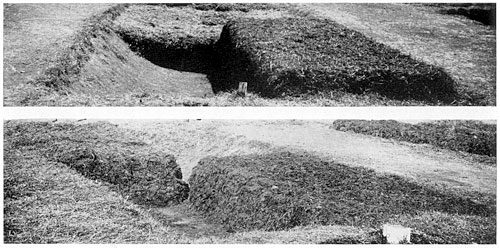
Plate IX. Turning the Compost: (1) First turn; (2) Second turn
|
Second turn.
One month after charge (Plate IX). The water required is about three tins. The material is cut vertically in two inch slices and piled up with watering as before along the empty half of the pit. The material should fall loosely, under each stroke of the spade and not in lumps, so as to ensure copious aeration. The third and fourth waterings, 1.5 tins each, are given five and six weeks after charge.
Third turn.
Two months after charge (Plate X). About two tins of water are necessary. A rectangular heap is made on the ground alongside the pit or in the field, not more than 10 ft. broad at the base, 9 ft. wide at the top and 3.5 ft. high, the material being spaded and piled with watering as before. (When the heap is made in the field, all the water needed should be added at the time of carting.) The contents of several pits may now be placed side by side to save space, to economize water and to facilitate removal. The fifth and sixth waterings, 1.25 tins each, are given nine and ten weeks after charge. For the first time during the process, extra labour, namely three men and four women for six hours, is required for each pit at the third turn. As the heap can be made either in the factory or in the field, this additional labour can be debited to the application of the humus to the land.
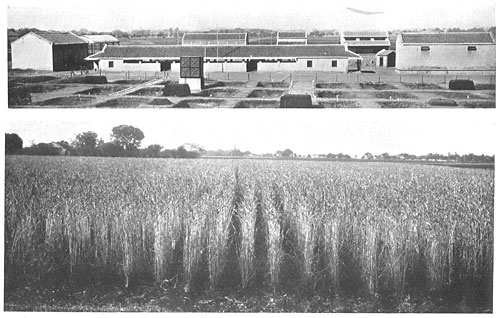
Plate X. (1) General view of the Compost Factory at Indore. (2) The effect of Compost on wheat.
|
Three months after charge the manure is ready, when it should be applied to the land. If kept in heaps longer than three months after charge, nitrogen is certain to be lost. There is no great harm in putting the manure on the land after two months if urgently required, especially when the process has run for some time and everything is in full working order.
Time-Table of Operations
The complete time-table of the manufacture of compost, which takes ninety days, is given in Table V.
Table V
The Complete Time-table for One Compost Pit
|
Day
|
Event
|
1
|
Charging begins.
|
6
|
Charging ends.
|
10
|
Fungus growth established.
|
12
|
First watering.
|
16/17
|
First turning, compost inoculated with bacteria from another pit thirty days old.
|
24
|
Second watering.
|
30/32
|
Second turning.
|
38
|
Third watering.
|
45
|
Fourth watering.
|
60
|
Third turning.
|
67
|
Fifth watering.
|
75
|
Sixth watering.
|
90
|
Removal to field.
|
Output
Fifty cart-loads of ripe compost per pair of oxen per annum can be made from the plant residues available on any holding. The quantity can be more than doubled when all the dung and urine earth are used, provided of course sufficient vegetable refuse can be secured. Fifty to seventy-five tins (200 to 300 gallons) of water, according to the season, are sufficient to make one cart-load of finished compost. No extra labour is required other than that usually employed in the cattle-shed, namely two men and three women. These are sufficient for the work connected with forty oxen and the preparation of 1,000 carts of compost per annum.
The labour needed for the annual manufacture of 1,000 cart-loads of compost has been reduced to a minimum by: (1) the provision of a water supply; (2) the general design of the cattle-shed and compost factory and (3) the detailed training of the labour force to carry out the work quickly and without unnecessary fatigue. This aspect of the manufacture of humus has been greatly assisted by the system of managing labour adopted at the Institute (Appendix D).
During the year 1930, when 840 cart-loads of compost were prepared, a careful record of the actual time spent on compost making by the labour employed to look after the work cattle, was made. It was found that one half of the time of this labour was spent on the care of the cattle and one half on the making of compost. The total wages debited to actual compost making came to Rs 441.5, i.e. to 8.5 annas, or ninepence halfpenny, per cart-load of finished material. During the present year, 1931, the output has increased and is expected to reach 1,000 cart-loads. It is best to spread the compost on the land directly it becomes ready, so as to facilitate the distribution of farm work throughout the year.
Manurial Value of Indore Compost
One cart-load of Indore compost is equivalent, as regards nitrogen content, to two cart-loads of ordinary farmyard manure. Properly made compost has another great advantage over ordinary manure, namely its fine powdery character which enables it to be uniformly incorporated with the soil and to be rapidly converted into food materials for the crop. Taking everything into consideration, Indore compost has about three times the value of ordinary manure. The crops of irrigated wheat and sugar-cane, raised on land which has been graded and afterwards manured with compost, are shown in Plates X and XI.
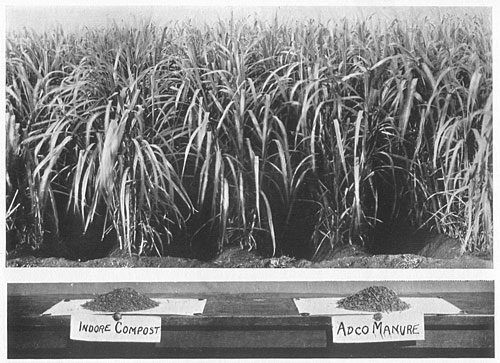
Plate XI. (1) The effect of Compost on sugar-cane. (2) Compost made by the Indore and Adco methods.
|
Next: 5. The Chief Factors in the 1ndore Process
Back to Contents
To Albert Howard review and index
Back to Small Farms Library index
Community development | Rural development
City farms | Organic gardening | Composting | Small farms | Biofuel | Solar box cookers
Trees, soil and water | Seeds of the world | Appropriate technology | Project vehicles
Home | What people are saying about us | About Handmade Projects
Projects | Internet | Schools projects | Sitemap | Site Search | Donations | Contact us