
Search the Journey to Forever website click HERE

En español
Biocombustibles, biodiesel
Navigation
|
Washing
Spanish version -- Versión en español
Why bother?
Which washing method is best?
Mist washing
Bubble washing
Oxidation and polymerisation
Stir washing
Washing tanks
Settling and separation
The washing process
Recycling the wash-water
Washing temperature
Emulsions
Using acid
Wash-water disposal
Drying the fuel
Dry-washing
Why bother?
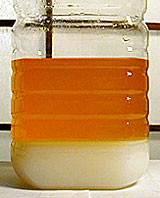
Milky water after the first wash...
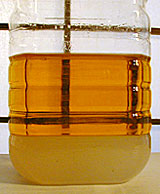
2nd wash -- murky water...
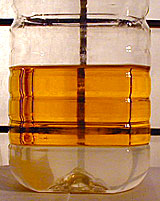
3rd wash -- clear water at pH7, clear biodiesel on top
|
Frequently Asked Question: "Do you really need to 'wash' biodiesel? I've been running a 50/50 biodiesel/petro diesel mix for a few months so far and my Dodge Cummins runs great on it."
Answer: Yes, you do really need to wash it. A can of HEET "DriGas" fuel antifreeze (methanol) in the tank every once in a while to deal with a water problem doesn't do any harm, but constant exposure to the excess methanol in unwashed biodiesel won't do the fuel-system hoses and seals any good. Free glycerin and sodium or potassium soaps in the fuel will do harm -- it's only a matter of time. "A few months so far" isn't very long in the life of a diesel engine -- nothing's ever broken until it breaks.
Read what the Fuel Injection Equipment (FIE) Manufacturers (Delphi, Stanadyne, Denso, Bosch) have to say about the contaminants left in unwashed biodiesel:
Summary -- html
Full document -- Acrobat file, 104kb
See: Determining the Influence of Contaminants on Biodiesel Properties, Jon H. Van Gerpen et al., Iowa State University, July 31, 1996 -- 12,000-word report on contaminants and their effects. Acrobat file, 2.1Mb
Quality biodiesel must be washed.
Frequently Asked Question: "I don't wash my biodiesel, but I filter it through an automotive oil filter, then through a 3-micron oil filter, this is after allowing the biodiesel to settle in a 55-gallon barrel for a couple days. Is this adequate?"
Answer: No. Settling and filtering will not remove the soap, catalyst, glycerin or excess methanol contaminants.
Frequently Asked Question: "Methanol is good fuel, why wash out the excess methanol, what a waste!"
Answer: Methanol is good fuel only in specially prepared race car engines, which are not diesels. Excess methanol in unwashed biodiesel is not good fuel and does harm, corroding the fuel injection system. Wash it out of the fuel.
Which washing method is best?
Frequently Asked Question: "I was wondering if anyone could tell me which way might be best for washing large batches of biodiesel? I was wondering if bubble washing or top-mist washing would be better." -- Biofuel mailing list, July 2004
Answer: Neither.
First you have to know what an emulsion is and why it matters. Briefly (more below), oil and water don't mix, and well-made biodiesel should separate quickly and cleanly from the wash water when it settles. But if the biodiesel isn't made properly it will contain half-processed oil molecules -- monoglycerides and diglycerides (MGs and DGs), which are emulsifiers. Emulsifiers are used to make stable mixtures of oil and water, such as mayonnaise. If there's too much of it in your biodiesel, some of the biodiesel or all of it won't separate from the wash water, or at least not quickly, and in some cases maybe not for weeks. You have an emulsion problem.
In fact it's a quality test -- if it doesn't separate, you need to improve your processing. Properly made biodiesel with good reaction completion will not emulsify.
You can "fix" an emulsion, or prevent it forming (see below), and emerge successfully... but with poor-grade fuel. The emulsifiers are fuel contaminants, they can't be washed out, and the upper limits for them in the national standards specifications are low. Above those limits they'll cause injector coking and damage your engine, especially with prolonged use.
Gentle and super-gentle washing techniques like bubblewashing and mist washing simply mask the problem that the fuel may not have been made properly in the first place.
"Mist- and bubble-washing have become 'institutionalized' amongst some homebrewers , mainly because of the frequency of incomplete reactions that lead to washing problems. They are both methods of treating incomplete reactions with kid gloves in the hopes that any resulting emulsion won't be 'too bad' or 'too noticeable.'
"No wash method should be used on any batch unless it is known for certain that the reaction has completed (see Quality testing). Unfortunately, many people fail to guarantee this for themselves, opting to just 'go ahead and wash it gently'."
-- Todd Swearingen. Biofuel mailing list, July 2004
Quite so. See below, Stir washing.
There is a lot of confusion about this. Here's a different reply to the same message, from a champion of super-gentle washing methods:
"Either mistwash or bubblewash works fine for big batches, but the same rules apply as for small batches -- more water is needed for misting and less emulsification happens, much less water is needed for bubblewashing but more chance that emulsification can take place.
"I actually use both now -- mist for a few gallons and then I bubblewash with good use of water recycling during bubblewashing. In my 350-gallon wash tank, my small aquarium air pump gives fine results, but not all of the air pumps might be able to handle such large batches. It looks like a tiny amount of bubbles are rising but it works really well -- less emulsification than the same air pump agitating up a smaller batch."
-- Maria "Girl Mark" Alovert, July 2004
But what sort of fuel will emulsify at all in a 350-gallon tank with only a small aquarium air pump to "agitate" it? Well-made biodiesel can take violent washing with a high-speed paint-stirrer without emulsifying, you can't emulsify it with an aquarium air pump.
Strangely, Ms Alovert had previously said this about bubblewashing:
"The bad news is that poor-quality biodiesel can emulsify just from the agitation of bubblewashing. The good news is that it's easy to make good biodiesel... Some people use a super-gentle 'mist washing' method to take vigorous agitation out of the picture. To me it seems that this masks the real problem -- which isn't agitation, it's poor fuel quality. I'd rather make sure I've produced fuel that contains less soap and less emulsifying monoglycerides and diglycerides, instead of decreasing the agitation to 'ease washing'."
-- "Bubblewashing 101", Maria Alovert, 12 May 2003
But Ms Alovert was now using the sealed 200-litre hot water tank "Appleseed" reactor which she promotes, based on Dale Scroggins' excellent Touchless Processor design, and the 1" Clear Water pump she was using to agitate it is too small for more than 100 litres -- it won't mix a 200-litre tank batch thoroughly in the usual time allowed. Also, problems with the plumbing of the Appleseed reactor made separation of the biodiesel from the soapy glycerine by-product layer difficult. Poorly processed biodiesel that's contaminated with glycerine needs super-gentle washing methods.
But, as Ms Alovert said, it's easy to make good biodiesel. These problems are easily solved.
"I went from 1 & 2-liter test batches to a small 15-liter processor and all went fine. When I bumped up to a 30-gallon batch I got incomplete reactions and the emulsions during wash that can go with it. The washed and dried biodiesel looked great, but produced more glycerine when a sample was reprocessed. Following advice from Keith Addison at Journey to Forever I scaled down the volume of the batches, increased the temperature a few degrees, and increased processing time. It is often necessary to tweak the process as you scale up. It is much easier to wash good quality biodiesel. It takes less time and it's less expensive to process it right the first time than to have to reprocess a batch."
-- Tom Kelly, Biofuel mailing list, 5 October 2005
Tom left emulsions behind and now uses stir-washing (see below). We also use stir-washing, as do many others. We make biodiesel all the time, but it's many years since we saw an emulsion at Journey to Forever.
Mist washing
Mist-washing uses a fine spray above the wash-tank to send a mist of water droplets down onto the surface, creating zero agitation. It works, or anyway it does wash the biodiesel, though it's slow and it uses a lot of water, and usually the water is not re-used.
Why do it? After all, the basic quality test for biodiesel is to shake it up violently with some water in a jar and see how long it takes to separate (see Quality testing). If you can't agitate it during the wash without it foaming up or forming an emulsion then go back to the beginning and learn how to make the fuel properly. Then you can use more effective washing methods that won't just mask poor processing.
Bubble washing
Bubble-washing was developed at the University of Idaho and gained widespread popularity among home-brewers. It uses a small air-pump, usually an aquarium aerator pump with a bubble-stone. Water is added to the biodiesel in the wash tank (usually a quarter to a half as much water as biodiesel); the water sinks to the bottom. Throw in the bubble-stone, which also sinks to the bottom, and switch on the pump. Air-bubbles (lots of little bubbles is best) rise through the water and into the biodiesel, carrying a film of water around them, which washes the biodiesel around the bubble. When it reaches the surface the bubble bursts, leaving the water to sink back down again, washing the fuel a second time.
Usually three or four washes are used, each of six to eight hours, often less for the first wash, with a settling period of at least 1 hour between washes (some people settle it for much longer). After it's settled the water is removed via a bottom-drain and replaced with fresh water.
Washing is completed when the water is clear after settling, with a pH of 7 (or the same as your tap-water).
Some of the cheaper air-bubble stones aren't biodiesel-proof and can crumble away any time from immediately to soon, especially the blue ones.
Get ceramic stones, they'll last indefinitely. A rough-grade carborundum stone will also work, or a pumice stone, though you'll have to weight it.
Advantages of bubble-washing: It's easy, it works, it doesn't take much effort -- add the water, switch on the aerator, come back later, do it again. For added convenience add a timer to switch off the air-pump after eight hours so you don't have to come back until a couple hours later (or a week later if you like) when it's settled and you can just change the water.
Disadvantages of bubble-washing: It might not take much effort but it takes a lot of time -- there are quicker (and better) ways (see below).
Bubble-washing is gentle and can mask an incomplete reaction, which agitation will reveal immediately. (Always do a wash-test first by shaking up a quarter or half a litre of the fuel with some water in a sealed jar or a PET bottle and see how long it takes to separate.)
Oxidation and polymerisation
A more complicated problem with bubble-washing is fuel oxidation.
All oils are not the same. Some are 'drying' oils, such as linseed oil, which is why it's used in paints and varnishes. When it dries the oil irreversibly polymerises (polymerizes) into a tough, insoluble, plastic-like solid. At the high temperatures in diesel engines the process is accelerated. Steadily accumulating films of tough, insoluble, plastic-like solids are not what you want in your engine and injector pump.
Polymerisation happens when the double bonds in unsaturated oil molecules are broken by oxygen from the air or water. The oil oxidises, forming peroxides (hydroperoxides), and the peroxides polymerise, bonding with carbon to create a long and stable molecule called a polymer (plastic). Another effect of oxidation is that the hydroperoxides attack elastomers, such as pump seals.
Without oxygen the oil can't polymerise.
Oxidation and polymerisation don't only affect the drying oils, there are also semi-drying oils, many of which are commonly used to make biodiesel, including sunflower and soy.
Saturated oils don't polymerise, unsaturated oils do. The level of unsaturation is called the Iodine Value (IV) -- the higher the IV, the more unsaturated the oil, the faster it will oxidise and the more it will polymerise. Linseed oil, tung oil and some fish oils have IVs of between 170 and 185. Coconut oil has an IV of 10 and won't polymerise. More information on IV here: High Iodine Values
Converting unsaturated oils to biodiesel lessens the polymerising effect but doesn't prevent it.
Mixing biodiesel made from high-IV oils with biodiesel made from lower-IV oils also lessens the polymerising effect but doesn't prevent it.
The Euro standard for biodiesel, EN 14214, is the de facto world standard. It sets both a maximum IV limit and an oxidation stability limit. The IV limit is 120, which excludes soy oil and sunflower oil as feedstocks for standard biodiesel in Europe, but includes rapeseed oil, the main oil crop in Europe.
Soy is the main oil crop in the US, and the US ASTM D6751 standard sets no IV limits.
In a paper published in 1996, leader of the Iowa State University biodiesel project Prof. Jon H. Van Gerpen stated: "The specification for biodiesel should include a limit on the tendency of the fuel to oxidize and a limit on the maximum degree of oxidation allowable for use of the fuel in diesel engines." See: Determining the Influence of Contaminants on Biodiesel Properties, Jon H. Van Gerpen et al., Iowa State University, July 31, 1996 (Acrobat file, 2.1Mb)
A November 2005 report by the Southwest Research Institute for the National Renewable Energy Laboratory of the US Dept. of Energy, An Evaluation and Comparison of Test Methods to Measure the Oxidation Stability of Neat Biodiesel, proposes test methods suitable for the inclusion of oxidation stability limits in the US ASTM D6751 biodiesel standard specifications. Acrobat file, 816 kb:
http://www.nrel.gov/vehiclesandfuels/npbf/pdfs/38983.pdf
The issue is still widely ignored or denied in the US (though there is now provision in the ASTM standard for on Oxidation Stability limit of 3 hours).
The European results are conclusive -- even when made from rapeseed oil with its lower IV, well within the EU standard limits, oxidised biodiesel can polymerise and damage pumps and engines. Anti-oxidant additives for biodiesel sell well in Europe.
Homebrewers and oxidation: Many homebrewers in the US think biodiesel shouldn't be used in the newer TDI or PDI diesel engines, because they think the high injection pressures will cause polymerisation. High pressures cannot cause polymerisation, only oxidation can do that.
Others think that if the biodiesel meets the US ASTM standard it will not polymerise -- but the ASTM standard sets no limits for IV levels.
"I agree with Mike Briggs [Biodiesel Group, University of New Hampshire] on polymerization. If we are talking about ASTM fuel, then it is a non-issue... Polymerization was pretty much dismissed at at least one session at the NBB [US National Biodiesel Board] conference in February of this year, as biodiesel performed far better than anticipated in the lecturers' tests... Meanwhile, quality control is not enforced in this country, so what do you expect?"
-- Kumar Plocher, owner, Yokayo Biofuels in California, "Concern over Bio polymerization", BioDieselNow Forums, 21 October 2004
Any problems there may have been with TDI/PDI engines using biodiesel in the US could be due to poor fuel quality, and could also be due to oxidation and polymerisation of high-IV soy biodiesel. But the problem is unacknowledged or denied. (See also The TDI-SVO controversy.)
From another discussion, at the "wastewatts" group at Yahoo, "Biodiesel, comparison of oils", 2 May 2006:
"Is there any one out there that has experience with using different oils and comparison of results when making biodiesel? I have been using Canola oil [IV 98] for the last 3 years, but now need to find another oil supply in addition to the canola I am getting. Have found Soya [IV 130] and Cotton seed oil [IV 105] users. So would like to know what to expect if I was to start processing these oils?" -- Trevor
Replies:
"There is no difference between soy, canola, cotton or the myriad of other oils."
-- Steve Spence, Green Trust Sustainability & Renewable Energy
"There's a comparison of various vegetable oils on the journeytoforever.org site [linked] that details the cetane ratings, melting points, Iodine Value, and oil yields from seed and nut crops. High Iodine Values are reportedly associated with polymerisation and subsequent possible engine damage (not just when using SVO but biodiesel made from these oils as well). A link within this page references the Euro standard for biodiesel, EN 14214, which sets the maximum Iodine Value (IV) at 120. The IV level of 120 reportedly includes rapeseed oil but excludes soybean and sunflower oil as sources of standard biodiesel in Europe. ASTM standards in the United States don't set Iodine Value limits."
-- Rosannah
"Very thorough article. Nice find!"
-- tinkerbill (william)
"The key word being 'reportedly'. In reality, when picking up used fryer oil from a variety of sources, it tends to average values out and there are no real world issues."
-- Steve Spence, Green Trust Sustainability & Renewable Energy
In reality, mixing oils with different IVs or mixing the biodiesel made from them has no effect on the IV or the oxidation stability of a higher IV oil: if it is oxidised it will polymerise no matter what other biodiesel you mix it with. Different IVs are not "averaged out", and most biodiesel homebrewers only have one source of used oil anyway.
Iodine Values are not "reportedly" associated with polymerisation, they ARE associated with polymerisation. And there have indeed been "real world issues" in the shape of damaged engines.
All oils are not the same.
Another issue remains ignored -- the hydroperoxides formed in high-IV biodiesel when it oxidises are much more likely to rot elastomer injector seals than biodiesel is.
Oil paint is based on high-IV vegetable oils. Paint doesn't dry when it's in the paint tin with the lid sealed. It does dry if you paint a thin film of it on a surface exposed to the air.
Biodiesel tends to cover everything it touches with a thin film. When motors stand idle overnight or longer, thin films of biodiesel cover many engine parts, including elastomer seals.
This isn't exactly scientific, but you could try painting a thin film of your biodiesel on a piece of glass, or any clean, smooth surface, along with a thin film of the oil you made it from, see if it starts getting sticky to the touch and dries. Pour about 1/8" (2-3mm) of your biodiesel into an uncovered shallow dish and keep an eye on it, watch for it turning a reddish colour, darker and more viscous. If it happens, check how long it took. You might want to consider finding a source of better oil.
If you're using a higher-IV oil for biodiesel, make it well, store it well, and use it soon.
See also Storing biodiesel
Bubble-washing and oxidation: Without oxygen the oil can't oxidise and polymerise. Everyone knows what a fish-tank aerator does: it pumps the water full of oxygen so the fish can breathe. Bubble-washing does the same thing to biodiesel, pumping it full of oxygen.
Bubble-washing certainly increases oxidation. We've been sent some lab test results from Europe, or rather a precis of them. The home-brewed WVO biodiesel tested passed all the standards requirements except the Oxidation Stability level. Those home-brewers no longer use bubble-washing for their fuel. They use high-speed stirrers.
If you do use bubble-washing, use the fuel quickly, especially if your feedstock was soy or sunflower oil or another semi-drying oil. Storing it for a long time might not be a good idea. There are a lot of variables: the kind of oil you used, how you store it, the weather... Keep it airtight in full containers in a cool, dark place. There are also anti-oxidant additives which you could try. We have no experience of them. With semi-drying or higher IV oils, try alternating or mixing with batches of biodiesel made from lower IV oils in your tank.
We don't use bubble-washing, we use a paint-stirrer in a high-speed drill (see next).
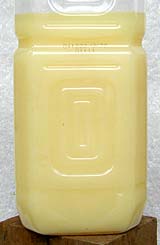
Stir-washing, the first wash -- homogenised biodiesel and water immediately after a thorough mix with a paint stirrer.
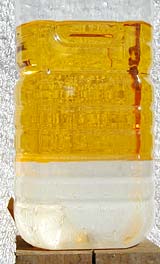
3rd wash -- clear water at pH7, clear biodiesel on top, no loss of yield.
|
Stir washing
Frequently Asked Question: "Is there a way to speed-up the water-biodiesel wash? I've read the bubble-washing techniques and understand it, but for the best quality of biodiesel, it can take up to a week, with several washes."
Answer: You can speed up the washing process considerably. Here's how:
1) Throw out your mist washer.
2) Throw out your bubble washer.
3) Never try to wash an incomplete reaction -- test-wash a sample first. (See Wash-test.)
4) Use a motor-driven impeller (eg a paint-stirrer in an electric drill) to mix the water/fuel mixture for about 5 minutes, until it looks homogenous.
5) Let it settle for 1 hour.
6) Drain the water from the bottom and repeat steps 4, 5 and 6 two more times.
7) Let the fuel air-dry or heat it to 120 deg F (48 deg C) to dry.
Depending upon the volume of oil in your batch and the power of the impeller, you could get your entire batch process time down to 24 hours.
Many people avoid mechanical mixing of the fuel at the wash stages, thinking that it will create emulsion problems. And they're right if they try to wash 'fuel' from incomplete reactions. -- Todd Swearingen, Biofuel mailing list.
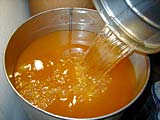
Stir-washing a 60-litre batch -- in goes the first wash water, 20 litres of it.
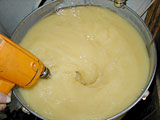
A paint-stirrer on a drill agitates the whole tank (avoid making a vortex, but it helps for photographs!).
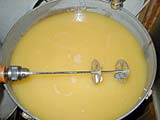
The double paint-stirrer. Three washes in a day leaves the biodiesel clean and clear, with no emulsion formed and no loss of yield.
|
Comments:
- "Todd, I had a chance to try your 'fast' wash method today (35 gal white poly drum) with a simple 55 gal drum mixer and wanted to thank you for the time you just gave back to me! Success! At least for me, it's much better and faster to wash biodiesel this way, compared to the bubble-wash method. Just five minutes of 'appearing homogenous' and allowing the 1 hour settling, drained-off and replaced the water and repeated for a total of three wash cycles. The water and biodiesel layers are currently clear and it's settling for 24 hours. Excellent separation, no emulsion!" -- Kevin Shea, Biofuel mailing list.
- The higher the quality of biodiesel the more rigorous the wash agitation can be. The batches that I have made that cannot take stir washing (emulsions occurred) have invariably been the result of incomplete reactions. As the biodiesel I make has increased in quality, it has stir washed very easily. -- Tom Kelly, Biofuel mailing list.
Advantages of stir-washing: Quick and effective, no masking of a poor reaction, no oxidation.
Disadvantages of stir-washing: There aren't any. BUT you have to process the fuel properly in the first place. Some beginners have difficulty with this, all seems well until they start the wash, and hit problems -- it foams, or it turns into "chicken soup" or "mayonnaise" and won't separate from the water. And then they get discouraged.
Don't be discouraged, keep trying! It's just a matter of practice and getting a good feel for the biodiesel process. Make sure your titration and measurements are accurate, be as meticulous as you can, make sure your chemicals are fresh and high-quality, that you're processing the fuel at the right temperature and agitating it for long enough. Make small test batches for comparison -- see Poor man's titration.
More advice:
"You can use a propellor agitator [eg a paint-stirrer in a drill] for about 5 minutes, enough to homogenize the fuel and water, and 99% of the water will settle out in an hour. You could probably conduct one wash every three hours. Leave the last wash to settle 12-24 hours before drying the fuel.
"Some people express concern with pump-washed or propellor-washed fuel not clearing as quickly as mist- or bubble-washed. There's sound reason for this. Pumps and propellors mix the fuel and water better, 'atomizing' it. This means greater surface-to-surface contact between water molecules and all suspended or dissolved impurities. A total of 15 minutes with a 1/2 hp motor and 4"-6" propellor in a 200-gallon wash tank or bigger will achieve the same thing or more as an all-day affair with a mist-washer or bubble-washer. This allows for hours of washing time to be converted to settling time, in turn hastening the entire wash process.
"Pump washing atomizes the two fluids more quickly and thoroughly than propellor washing and can generate an emulsion in washing biodiesel with poor reaction completion."
-- Todd Swearingen, Biofuel mailing list
As long as the reaction completion is good, you can use the same pump you use for the biodiesel reaction to wash the fuel. It might save some money but before you process your next batch you'll have to flush the pump out thoroughly with biodiesel. The same goes for using the reactor vessel as a wash-tank. It is an option if you're short of space, but having a separate wash-tank with its own stirrer is a much better option.
If you use a sealed water-heater tank as a reactor, there'll probably be residues of soapy glycerine by-product that didn't drain left in it to foul up the washing process, and the wash process will leave traces of water to foul up the next biodiesel batch. Get a separate wash-tank.
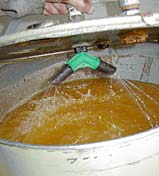
A revolving garden sprinkler does a good job of mixing fuel and water. Water is drawn from the bottom of the tank and sent to the sprinkler via a small pump.
|
(If you do happen to get some by-product in the fuel when you're transferring it to the wash-tank, let it all settle again overnight in the wash tank, then add up to a quarter as much hot water as biodiesel, pour it over the surface of the fuel. Let it settle for a few hours and drain off the water.
Do a wash-test -- see Quality testing. If the fuel separates quickly from the water, continue with washing the batch as usual. If not, treat again with hot water, or use a gentle washing method.)
An alternative to stir washing is to use a small pump and a garden sprinkler (right). This has nothing in common with top-mist washing, there's nothing very gentle about it -- it homogenises biodiesel and water the same as mechanical stirring does though it takes a bit longer, about 15 or 20 minutes. It splashes a bit, but the danger of oxidation is very much lower than with bubble-washing's millions of little air-bubbles.
Washing tanks
You need a separate washing tank. If you have the space have two wash tanks, it really increases your production options. If you're short of space you can compromise by forcing the reactor vessel to serve as a washing tank as well (see above), but don't expect to like it -- a separate wash tank is a much better option.
The wash tank should be the same size as the processor tank or bigger. We wash 60-litre batches in 90-litre tanks, with 1/3 water v/v oil for each wash, ie 60 litres of biodiesel and 20 litres of water. That leaves a few inches of headroom, enough for stirring or sprinkling or bubbling. (See photographs in Stir washing section, above.)
The tank should have a bottom drain fitted with a valve. Cone-shaped tank bottoms help, but it also helps if it's convex, which you can achieve by standing a flat-bottomed tank on a few bricks under the bottom edge (which is usually a lip) and bashing the bottom down a few millimetres with a heavy bit of lumber wood. Often the drain fitting has a raised edge a millimetre or so above the floor of the tank, which is annoying but you can live with it.
If there's no bottom drain and it's a closed drum there should be filler caps in the lid and one of them might take the standard plumbing fitting thread on a 3/4-inch ball valve or gate valve. Closed 200-litre 55-gal drums have two caps, one with a standard 3/4" thread. Cut the bottom of the tank out instead of the top and turn the tank upside down, fit a drain valve to the cap.
Otherwise cut a hole for the drain and weld a female-threaded valve fitting into place. Use the fitting to mark out the size of the hole and carefully drill a circle of small holes, maybe 2mm, right next to each other just inside the circle. Cut through the remaining metal between the holes, remove the inner bit of metal, and use a half-round file to file the edges of the hole smooth until it fits the valve fitting. If you do it carefully you should be able to screw the valve fitting into the hole. Then weld or braze the fitting in place.
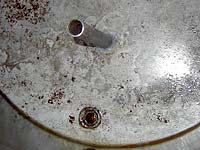
The washing tank stand-pipe -- inside the tank, with the stand-pipe above, the ordinary drain below.
|
We use standpipes in our wash tanks, with two drain outlets. One drain has a length of pipe inserted into the outlet inside the tank, calculated so that the open end of the pipe is higher than the depth of the settled wash water in the bottom of the tank.
The wash water is drained from the ordinary outlet for the first washes, but after the final wash has settled, we use the standpipe outlet to drain the biodiesel before draining the wash water, which makes certain you don't get any of the water along with the biodiesel. Then the water is drained from the ordinary outlet along with the remaining biodiesel, settled again, and the biodiesel poured off from the top.
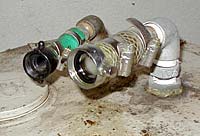
Wash tank lid, on the right the hose-barb connection for the transfer pipe from the settling tank. The other fitting is a water inlet but we never use it -- we use 20-litre (5-gal) steel pail to load the water into the tank.
|
Lids: You can make a lid for the tank from a piece of compound board cut to fit with sheet plastic glued on the underneath surface and four toggle latches. Give it a silicon seal too if you like -- apply a generous helping of silicon round the underside edge, allow to set for 6-8 hours (depending on the weather) until it isn't sticky to the touch anymore but is still soft. Then place the lid carefully in position on top of the processor and weigh it down with something heavy, making sure the weight is spread evenly around the edge. The silicon takes the shape of the rim but doesn't stick -- no need for a release agent.
Rig a stand for the wash tank that's high enough for a bucket to fit easily under the outlet valve. We use steel stands cut and welded from angle iron. Consider that a 200-litre 55-gal steel drum with a batch of biodiesel and wash-water weighs about 350 lbs, 160 kg, don't use a flimsy or wobbly stand for it.
Settling and separation
After processing, settle for at least 12 hours, preferably 24 hours, before separating the glycerine by-product and starting with the wash.
Be careful separating the by-product layer from the biodiesel, it's very soapy stuff -- much rather have some biodiesel in the by-product than by-product in the biodiesel when you want to wash it.
If you do happen to get some by-product in the fuel when you're transferring it to the wash-tank, let it all settle again overnight in the wash tank, then add up to a quarter as much hot water, pour it over the surface of the fuel. Do a wash-test -- see Quality testing. If the fuel separates quickly from the water, continue with washing the batch as usual. If not, treat again with hot water, or use a gentle washing method.
We use standpipes to separate the glycerine by-product from the biodiesel (see caption) -- this is the best way, ensuring 100% separation, with all the by-product left behind.
The washing process
Transfer the biodiesel from the settling tank/processor, leaving ALL the glycerine by-product behind. Add water, wash.
Most people use 25% to 50% as much water as biodiesel or more for each wash. We use one-third as much, 20 litres of water and 60 litres of biodiesel.
Take no notice of advice that you have to pour the water in carefully and gently, that you mustn't pour it straight into the biodiesel, pour it against the side of the tank instead like you fill a beer mug or you might emulsify it. If you've used wash-tests to tune your processing and you test each batch before washing, just tip the water into the tank, it won't froth over like beer. Or pump it in through the lid.
The water sinks to the bottom. Proceed with the wash -- use the stir-washing method, see above.
Settle the fuel between washes for as long as you practically can before replacing the water and starting the next wash. Generally, the longer it settles, the more effective the next wash will be.
The first wash water turns white, like milk. Washing is completed when the water is clear after settling, with a pH of 7 (or the same as your tap-water), usually after the third or fourth wash.
Freshly washed biodiesel is often a bit cloudy. It should clear in a day or two. Leave it in a sealed container out in the sun, or heat it to 45-50 deg C (113-122 deg F) and let it cool in a vented container.
If the biodiesel goes cloudy again after it's cooled you probably haven't washed it thoroughly enough. Give it another wash, or if you're in a hurry, heating it to 45-50 deg C a second time might clear it. When it's clear go ahead and use it. See Drying the fuel, below.
If it doesn't clear, it probably needs reprocessing. Try the Reprocessing test and the Methanol test.
Recycling the wash-water
The counter-current method of re-using the washwater reduces water use for three washes by two-thirds.
The water doesn't become saturated with the contaminants it removes from the biodiesel. Instead an equilibrium is reached between the contaminants in the water and the contaminants still left in the biodiesel. Water from the first wash contains the most, with less in the second wash water and less again in the third. Water from the second and third washes can be re-used in washing your next batch of biodiesel. The second wash water is used for the first wash of the next batch, the third wash water for the second wash, with fresh water for the third wash. Only the water from the first wash is disposed of, and only when it has already been used for three washes in three successive batches of biodiesel.
Washing temperature
Washing is generally easier in summer than in winter, and the colder it gets the less effective the washing -- it takes longer and uses more water.
If your processor and wash-tank are in a heated room you shouldn't have any trouble. Otherwise, either heat the biodiesel or, easier, use hot water. Try to get the overall temperature to at least 30 deg C (86 deg F) or more. We use hot water in the winter. It's cheap for us, but it still uses energy, and energy isn't cheap no matter how little you pay for it. We have a Kyocera passive solar water heater, we just have to plumb it in, and then we'll use that.
Emulsions
Oil and water don't mix, and well-made biodiesel separates quickly and cleanly from the wash water when it settles.
But if the biodiesel isn't made properly and the reaction is incomplete it will contain half-processed oil molecules, monoglycerides and diglycerides (MGs and DGs), which are emulsifiers. Emulsifiers are used to make stable mixtures of oil and water, such as mayonnaise. If there's too much of it in your biodiesel, some of the biodiesel or all of it won't separate from the wash water, or at least not quickly, and in some cases maybe not for weeks. You have an emulsion problem.
In fact it's a quality test -- if it doesn't separate, you need to improve your processing (see Quality testing). Properly made biodiesel with good reaction completion will not emulsify.
The first thing to think about is why it happened so you can prevent it happening next time -- make good fuel!
The second thing is how to save the batch. One batch of sub-standard biodiesel won't hurt your motor (though constant use of it will), so rescue your bad batch and use it. Best to mix the bad batch in with better batches in your fuel tank.
A mild emulsion makes a third layer between the biodiesel and the wash-water after your first wash has settled. A paper-thin layer is fairly normal, just go on with the second wash. Thicker layers are not normal. Drain the layer off, with a bit of water and biodiesel on either side, and set it aside to settle, it will eventually separate. Heating it will usually separate it. Then leave it to dry, and add the top layer to your next batch of oil for reprocessing. Meanwhile continue with the second wash, which shouldn't produce an emulsion, or much less anyway.
A severe emulsion is when the entire tankful turns into a third-layer -- it looks like you have a tankful of chicken-soup or dirty-looking mayonnaise.
If you leave it overnight or for 24 hours it will usually separate, and again you'll be left with a third layer in the middle to deal with, as above. It might take longer to separate, several days or a week, especially in cold weather. Meanwhile your wash-tank is full of mayonnaise and you can't wash the next batch.
There are several ways of breaking the emulsion. Heating it will usually work -- 50-60 deg C (122-140 deg F) is usually enough. As with drying the oil before processing, if you use higher temperatures beware of causing steam explosions. Another way is to add hot water to the mix, if there's enough headroom in your wash-tank. The hotter the better. That should at least start the separation process: allow it to settle, drain off any water that's separated, add more hot water, and so on.
Another way is to add ordinary table-salt, sodium chloride. Dilute the salt in water first, add while stirring gently, keep adding until it starts to separate.
This works well to break the emulsion. But salt is an impurity that you should be washing out instead of washing in. It will take more washing than usual to get all the salt out and end up with clear, neutral water. And salty wash-water is not as innocuous as ordinary wash-water, so take care in disposing of it.
A third way is to use some acid to "quench" the wash, which will also break an emulsion. See next section.
Whichever method you used, once the emulsion is broken, continue with the rest of the washes until clear and dry as usual. Now you can use your rescued batch while pondering how to make better fuel next time.
Using acid
Some people say it's a mistake to "quench" the wash with acid. They say that while the acid will neutralize the alkali catalyst, it will also convert some of the soap to Free Fatty Acids (FFAs), which dissolve back into the biodiesel, and which you don't want in your fuel.
We don't use acid in the wash, but many people get good results using an acid quench. Some of them have had their biodiesel analysed, again with good results -- acid-quenched biodiesel can and often does meet and exceed standard specifications such as EN 14214 and ASTM D-6751. It's a normal procedure in commercial production.
Does it in fact convert soap to FFAs? Typical quantities of acid used are: 8 millilitres of 5% vinegar per litre of wash water used (usually a quarter to half as much water as the amount of oil used); 2 millilitres of 10% phosphoric acid per litre of washing water; enough ("not much") 5% phosphoric acid to bring the pH down to 7 (neutral). (Other acids used are sulphuric, citric or acetic, all well-diluted.)
This is how to convert soap to FFAs: Separating glycerine/FFAs. What it says is that for "average" WVO, titrating at 3 ml, you'd need 9.75 ml of 85% phosphoric acid per litre of oil used to convert the soap to FFAs, thus separating it from the glycerine. That's about 50 times as much acid as you'd use to quench the wash, and in the wash it's buffered by all that water too. FFAs? Naah.
But be sparing with the acid anyway.
An acid-quench will also break an emulsion or prevent it forming, which might disguise a processing problem that the emulsion would reveal. Always do a wash-test first! You can "break" an emulsion by slowly adding dilute acid (phosphoric, acetic, citric, or sulphuric, 10% concentration) until you see it start to separate (see "Emulsions", above).
NOTE: When diluting acid with water, always add the acid to the water, never add the water to the acid.
DudaDiesel Biodiesel Supply supplies concentrated acetic acid, citric acid, phosphoric acid and sulphuric acid, buy online: http://dudadiesel.com/.
Wash-water disposal
Wash-water is (or should be!) about as innocuous as the average family's laundry water.
Wash-water may contain the following:
Some biodiesel -- this is poor practice. The best way to avoid it is to use a standpipe in the wash-tank. Or, without a standpipe, when draining the wash-water, stop a few litres short of the interface with the first washes. With the final (3rd or 4th) wash, stop well short of the interface again, and drain the last of the water separately, along with some of the biodiesel. Let it settle in a separate tank. After a few batches' worth, syphon clean biodiesel from the top, dispose of the water.
Biodiesel is not an environmental hazard: US Environmental Protection Agency studies found that biodiesel is "more biodegradable than sugar and less toxic than table salt".
Some excess methanol -- most of the excess methanol is in the by-product, but some remains in the biodiesel and is removed with the wash-water.
The methanol can be reclaimed from the biodiesel, but it takes more energy than it recovers and it probably isn't cost-effective. For more information see Reclaiming excess methanol.
Methanol is poisonous, but only for humans and monkeys. Methanol is not viewed as an environmental hazard. According to the United Nations Environment Programme (UNEP), the International Labour Organisation (ILO) and the World Health Organization joint International Programme on Chemical Safety, methanol is readily biodegradable in the environment, it does not persist or bioaccumulate, it is not toxic to aquatic and terrestrial organisms and it does not have adverse environmental effects. See More about methanol.
The methanol in the biodiesel wash-water is not a problem for a waste-water treatment system -- in fact it might even be an advantage, some of the waste-water digester bacteria like it.
The lye catalyst -- potassium hydroxide (KOH) or sodium hydroxide (NaOH). See Soaps, below.
Sulphur (sulfur) -- if the acid-base process is used, the wash-water will contain some sodium sulphate or potassium sulphate salt. This is innocuous -- sulphur is one of the six plant "macro-nutrients" (nitrogen, phosphorous, potassium, calcium, magnesium, sulfur). It's essential for plant growth, all soils contain sulphur.
Soaps -- lye is commonly used as a drain-cleaner and presents no problems for waste-water treatment systems, and domestic waste-water contains much soap, also no problem for waste-water treatment.
Therefore, with good practices, wash-water can be disposed of as safely as domestic waste-water. Check with your local authority.
But this is treating the wash-water as a waste. There are better ways.
The wash-water can be treated with either magnesium sulphate (Epsom salts) or calcium hydroxide (both common chemicals), which will convert the water soluble soaps (sodium or potassium) in the water to insoluble magnesium or calcium soaps, which float to the top and can be collected. These soaps can be burnt as heating fuel.
The water should then be neutralised with dilute phosphoric acid. Now it contains potassium phosphates or sodium phosphates and can be diluted for use as irrigation water for pastures and fields (it needs more dilution with sodium than with potassium -- see Composting the by-product for more information on soil and plant nutrients).
The water can also be handled safely by means of a simple greywater system. There are many resources on the web to teach you how to do this.
Drying the fuel
When the fuel is clear -- not colourless but translucent, you can see through it, there's no haze or cloudiness -- then it's dry. Actually it's never dry: despite what the standards say, it always absorbs some water from the atmosphere, 1,200 ppm or more, but this is dissolved water, which is harmless, unlike suspended water, which must be removed.
It should clear by itself in a day or so after you separate the final batch of wash-water. Leaving it in the sun will help, or heat it to 45-50 deg C (113-122 deg F) and let it cool in a vented container. Most of the suspended water causing the cloudiness will evaporate off, and a little might settle out at the bottom. Water also condenses under the lid, careful when you take the lid off not to splash it back into the biodiesel. Or let it cool with the lid off.
If it goes cloudy again after it's cooled you probably haven't washed it thoroughly enough. Give it another wash. If you're in a hurry, heating it to 45-50 deg C a second time might clear it.
If it doesn't clear, it probably needs reprocessing. Try the Reprocessing test and the Methanol test. Work on improving your processing to achieve better process completion.
Another method is bubble-drying -- the same as bubble-washing but without the water. Drain the final batch of wash-water and use a bubble-stone and an aquarium air-pump to bubble air through the washed fuel. This will usually clear the fuel overnight. Sometimes it doesn't stay clear, in which case it might need another wash.
The disadvantage of bubble-drying is the same as with bubble-washing -- it oxidises the fuel, and you could have problems with the fuel polymerising unless you use it quickly. It won't pass the European EN 14214 standards requirements. We don't recommend bubble-drying for this reason. Our fuel is clear in a day or two anyway. Yours should be too.
Dry-washing
"Dry-washing" can be useful where water is scarce or expensive -- but it's not faster than ordinary high-speed stir-washing, and it's not "more efficient" either.
There are two types of dry-washing compounds:
Magnesol was the first dry-wash product on the market (and the company claims the term "dry-wash" as a trademark), but users say it's messy, and removing it from the biodiesel takes careful filtering.
More recent products are ion-exchange resins, which remove all impurities (salts, soap, catalyst, glycerine and water) from raw biodiesel following separation of the glycerine by-product.
The resin is placed in a special exchange column with a drain at the bottom, and the biodiesel is fed into the top. Ion-exchange resins can be cleaned (with methanol) and re-used, up to a point.
More information:
Using Ion-Exchange Resins For Dry-Washing Biodiesel
Top-quality DudaLite DW-R10 ion-exchange resin is available from DudaDiesel Biodiesel Supply: DudaLite DW-R10
Biofuels at Journey to Forever
Biofuel
En español -- Biocombustibles, biodiesel
Biofuels Library
Biofuels supplies and suppliers
Biodiesel
Make your own biodiesel
Mike Pelly's recipe
Two-stage biodiesel process
FOOLPROOF biodiesel process
Biodiesel processors
Biodiesel in Hong Kong
Nitrogen Oxide emissions
Glycerine
Biodiesel resources on the Web
Do diesels have a future?
Vegetable oil yields and characteristics
Washing
Biodiesel and your vehicle
Food or fuel?
Straight vegetable oil as diesel fuel
Ethanol
Ethanol resources on the Web
Is ethanol energy-efficient? |