
Search the Journey to Forever website click HERE

En español
Biocombustibles, biodiesel
Navigation
|
Biodiesel processors
Spanish version -- Versión en español
Introduction
Scaling up
Hazards
Test-batch mini-processor
Simple 5-gallon processor
Journey to Forever 90-litre processor
The 'Deepthort 100B' Batch Reactor
Ian's vacuum biodiesel processor
Chuck Ranum's biodiesel processor
"Foolproof" method processors
The touchless processor
Joe Street's processor
Continuous reactors
How to make a cone-bottomed processor
Biodiesel technology
Introduction
- "This is the first time I have ever in my half-century life attempted to build anything like this. I am VERY happy that I came across Journey to Forever. If I, with absolutely NO background in chemistry or hands-on tinkering, can produce a workable fully functional reactor/wash tank combo making top-rated fuel then anyone with sufficient determination and dedication can do it. Build your own, it is a VERY rewarding experience." -- Luc, Biofuel mailing list, October 2004
- "I'd like to start by reiterating what many have said about the Journey to Forever site, it's extremely informative, up-to-date and presents a wealth of information to novices (like myself) as well as to the veteran biodiesel brewers. After spending many hours researching biodiesel I found your site and really don't want to entertain looking elsewhere for information anymore. You have saved me a lot of time and money. I was about to purchase one of those pre-fab units till I read your archive mail list and looking at the Journey to Forever site for many hours, so now I'm planning on making my own reactor." -- Carlo Palermo, May 2007
- "I have converted others to the idea that they can do this without the 'Professional system'. We need to show people that this can be done with junk, it looks like junk, and runs like a top." -- Fred Finch, Biofuel mailing list, May 2006
Building your own processor isn't difficult. You don't need any special skills or special tools. There are plans, designs and ideas here to help you. There's also good information to be found in the searchable archives of the Biofuel mailing list discussion group:
http://www.mail-archive.com/biofuel@sustainablelists.org/
We don't recommend buying the ready-made cone-bottomed plastic biodiesel processors on sale at quite a few websites. They're overpriced, most of them don't work well, some are not capable of producing quality fuel, some of them have been prone to catching fire, most of them are not properly sealed, and they can't withstand much or any pressure, which is something that might happen.
One major plastic-reactor vendor, rather than including the separate washing tank that's a standard basic requirement, claims instead that washing biodiesel isn't necessary. Or you can pay another $1,000 for a plastic washing tank.
Some of these reactors don't even have a way of heating the oil (an electric heating band comes as an expensive extra).
In most cases you'd be paying a high price for a poor-quality processor that won't make good fuel and might not even be safe. You can build a better processor yourself, for much less money: "You could make an excellent processor plus more than 8,000 gallons of high-quality biodiesel for that price." -- From: Re: [biofuel] Best Processer, 14 June 2004
The processor designs that follow are for different types of processors. They can be used with any of the main processing methods and all of them will produce high-quality biodiesel efficiently.
These are the original designs, they're not copies of other processors, and many thousands of people have built them using the information presented here. They can be adapted to suit a wide range of circumstances -- there's a solution for everyone.
Only one design comes with precise blueprints, the others are built from recycled oil drums, water heaters, propane gas bottles, kerosene tanks (in our case), or whatever works -- they're designed to be adaptible to whatever is easily available.
Study all the designs before making your choices. The text will also give you essential information about processing techniques and how to make good biodiesel.
Note: Don't use copper tanks and avoid using copper parts -- not because the processing will damage the copper but because the copper will catalyse the oil. See Copper and SVO.
We've been using uncoated mild steel tanks for more than five years, with all the chemicals -- methanol, KOH and NaOH, concentrated sulphuric acid, occasionally phosphoric acid, also acetic acid, and they've produced hundreds of batches of biodiesel, but there's no sign of rust or corrosion yet.
Scaling up
Scaling up from small test-batches to a full-sized processor might not be straightforward. Your processing procedure might need some adjusting.
Processing instructions have to use averages and approximations to some extent because processors and conditions vary so widely. Short fat reactor tanks need more and better agitation than tall thin ones, using a pump for agitation might not be the same as using a stirrer and baffle plates, and stirrer speeds and blade configurations vary widely. Insulated tanks maintain better temperature control than uninsulated ones, some reactors don't have in-tank heaters and rely on insulation, etc etc.
All the processing methods provided at this website will get you close to the mark, then use the fuel quality tests to fine-tune your process to your particular processor.
You'll also need larger-scale measuring equipment. You'll be measuring methanol by the litre, not millilitres. We use a postal scale measuring up to 1,000 grams to weigh the lye for full-scale batches.
Mark out volume measures on the side of your processor or pre-heating tank for the oil. Heat some oil to the processing temperature (usually 55 deg C, 131 deg F), decant one litre into an accurate measuring flask, let it cool to room temperature and check the volume again. Multiply by 10. Using an accurate measuring flask, measure out this amount into a large bucket, mark the level in the bucket. Fill the pre-heating tank or the processor one bucket at a time, marking the tank as you go until you reach the right level for your processor's batch capacity of heated oil, whether 60, 80, 140 or however many litres. If you prefer, use 15 or 20-litre increments instead of 10 litres. For future batches, just fill the tank straight up to the level you've marked.
The main variables you'll face in scaling up are the amount of agitation, the duration of the process and the temperature. Adjust the rate of agitation and the process duration, stay with the usual process temperature and with your usual proportions of methanol and lye catalyst.
Agitation is usually via a pump or a stirrer. With stirrers you can vary the speed and the shape and configuration of the paddles, and you can use baffle plates in the tank.
With pumps, there's not much you can do to adjust the action. To take one example, the 1" Clear Water Pump from Northern Tools is a popular choice. Usually it's stepped down to 3/4", but then the maximum-sized batch it will handle efficiently in the usual processing time is about 80 litres (21 US gal), 100 litres at the most (26 US gal). Nonetheless these pumps are often used with 200-litre reactors (55 US gal), which can result in the washing problems that come with poor process completion. Using full-sized 1" fittings would help, but it might still need extended processing times. For 100 litres and more use a more powerful pump.
For temperature control, once the oil is hot it doesn't need much reheating during the processing, especially if the reactor tank is insulated. But accurate temperature control helps and a thermostat is useful (though not essential). It's also a safety factor -- if you forget to switch off the heating element the oil will get too hot and boil off the methanol, upsetting the process and building up pressure in the reactor. With a thermostat you can just set it to the required temperature, switch it on and leave it until the processing is finished.
Next to oil quality, the main variable in making biodiesel is user error, especially inaccurate measurements. Starting off with small 1-litre test batches not only means your mistakes are small ones, it's also the best way to learn good technique. Learn the process first, building the processor comes later. Start here.
Tweaking the process
From Todd Swearingen, Biofuel mailing list, 3 Sep 2004:
To judge the best reaction time, take a 200 ml sample of fluid out of the reaction stream every half-hour after an initial 1-hour reaction period. Let the sample settle.
The volume of the glycerol cocktail that settles out of each sample will give you a fair gauge as to when your reaction completed.
Continue the reaction for half an hour beyond the point where the glycerine cocktail volume stabilized.
From Tom Kelly, Biofuel mailing list, 27 Jan 2006:
I have been tweaking my process. I produced what seemed to be good biodiesel, but with the Methanol Test a very small residue would invariably remain undissolved in the methanol. I wasn't sure that it was possible to make BD that passed the test.
- I reduced the volume of oil to 20 gal (76L) (I use a 1" clear water pump for agitation).
- raised the temp to 150F (in a sealed water heater with vented pressure relief valve).
- increased the reaction time to 2.5 hrs.
- increased methanol from 4 to 4.5 gal.
With all of this I finally produced biodiesel that passed the Methanol Test.
I then went back to 4 gal of methanol (20% of Vol of oil). The biodiesel still passed the Methanol Test.
By-product separation: If you don't use stand-pipes or something similar to ensure complete separation or biodiesel from the glycerine by-product (see Stand-pipes), make sure to drain the biodiesel from the top, first. If you first drain the settled glycerine by-product from the bottom, and then continue to drain off the biodiesel through the same bottom drain, the biodiesel will contain some by-product: glycerine by-product is sticky stuff, after draining a thick coating of it is left sticking to the sides and bottom of the tank, which the much thinner biodiesel washes off and carries to the washing tank, where it will cause washing problems.
Hazards
The main hazards of making biodiesel are poisonous fumes, dangerous chemicals, and fires. For poisonous fumes, the best advice is not to expose yourself to the fumes in the first place. Don't use "open" reactors -- biodiesel processors should be closed, with a vent pipe leading safely to the open air outside. See Safety.
Here we'll deal with fires. There have been several fires, one operator lost all his equipment, and his shed, and he was slightly burned. But, as he admitted, it was due to his own carelessness (an open processor, and heating the oil with a direct flame) and shouldn't have happened. It's easy to avoid fires. Most important, again, use closed processors.
Always have a fire extinguisher handy -- dry chemical, carbon dioxide, water spray (fog) or foam. Do not use straight streams of water.
Good advice from the Biofuel mailing list:
The main fire hazard is using an open reactor with poor ventilation near an ignition source.
Ignition sources can be:
- Using combustible fuels as a direct heat source (propane, natural gas, wvo, wood, etc.), rather than a heat exchange system where the flame is removed from the processing area.
- Any open flame in the processing area.
- Open electric motor housings, rather than TEFC motors (Totally Enclosed Fan Cooled AC Motors) or explosion-proof motors.
- Using wall-plug connections instead of switches, poor-quality or under-specified electrical wiring, over-specified fuses, electrical wiring lying on the floor.
Oil-soaked rags can cause spontaneous combustion if not handled properly, especially when working with drying oils such as hemp and linseed. The threat decreases as the saturation of the oil/fat increases. (See Iodine values). Don't just leave oily rags in a pile, wash them with soap and water and dry them for re-use or before discarding them (or burn them, if they're not worth saving).
'Foolproof' processors
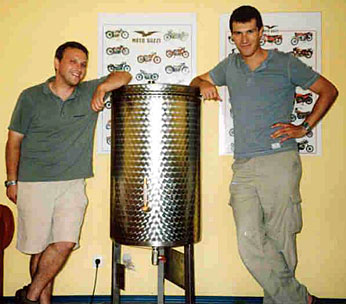
Aleks Kac (left) and friend Matevz with Matevz's beautiful round-bottomed stainless steel processor, built for the Foolproof method.
|
Bulk processor outline for "Foolproof" process
Applicable for almost any size
By Aleks Kac
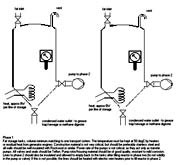 |
|
|
|
Click on pictures for bigger images |
|
|
|
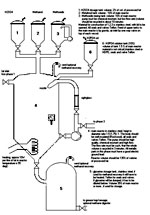 |
|
|
Phase 1 -- primary settling |
|
|
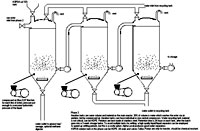 |
|
|
Phase 2 -- main reactor |
|
|
|
Phase 3 -- washing processor |
|
|
|
|
|
|
|
|
|
|
|
|
|
Touchless processor
Dale Scroggins's processor is "a 100-liter processor made from mostly salvaged materials that almost fills itself, mixes everything, recovers the unused methanol, washes and dries the ester pretty much by flipping a few switches... I first evacuate the tank, then suck in the oil through a filter setup that I'm a little too proud of. I mix the methoxide separately, using a drill press with a paint mixer installed, then suck it into the tank. Then flip the pump switch. Watch through the clear hoses and marvel. Later, flip off the pump switch, check for separation, flip on the vacuum pump (which is connected to a liquid trap which is connected to the condenser which is connected to the tank) and watch the excess methanol collect in the trap. When no more collects, I open the tank to the atmosphere and drain off the glycerine. Then suck in water and begin the wash." (From a message to the Biofuel mailing list, 11 Jan 2001)
Full description, more photos and drawings at Dale's website:
http://home.swbell.net/scrof/Biod_Proc.html
Joe Street's processor
This processor is made from a 36-liter hot water tank and employs vacuum which has many advantages in safety and reduced processing time.
Vacuum drying the oil ensures low water content, which is critical to a good process, and vacuum allows catalysts to be drawn into the processor rather than forcing them in by pressurizing containers. Vacuum allows fuel to be quickly dried at the end of the process as well giving considerable time savings from start to end of process. The reactor employs forced exhaust for safety and is designed to allow methanol recovery and two-stage processing without any additional modifications.
The design is easily scaled up in size, and makes quality fuel consistently, and easily. From the start, the purpose of this project was to offer something easily reproducible so that as many people as possible can have a chance to make their own fuel.
30-litre version -- full construction manual -- download here (6.9 Mb pdf)
90-litre version -- full construction manual -- download here (11.6 Mb pdf)
Process description for the single stage base catalyzed reaction on the vacuum reactor -- download here (60 kb pdf).
Advanced process description -- download here (60 kb pdf).
1500-litre version -- Rod Roth's vacuum reactor uses a sealed 500-gallon propane tank as the reactor vessel. It produced over 85,000 litres of biodiesel in the first year of operation. Pictures and details of "The Beast":
http://www.rsssrocksbc.com/freebiodieselreactorplansbyjoestreet.html
Make your own continuous reactor! Oscillatory Flow Mixing (OFM) provides highly effective mixing in tube reactors by the combination of fluid oscillations and baffle inserts ... OFM is particularly suited to continuous processing. How it works, Research, Technology, Publications, and more, with diagrams and photographs.
http://www.cheng.cam.ac.uk/
research/groups/polymer/OFM/
Next
Biofuels at Journey to Forever
Biofuel
En español -- Biocombustibles, biodiesel
Biofuels Library
Biofuels supplies and suppliers
Biodiesel
Make your own biodiesel
Mike Pelly's recipe
Two-stage biodiesel process
FOOLPROOF biodiesel process
Biodiesel processors
Biodiesel in Hong Kong
Nitrogen Oxide emissions
Glycerine
Biodiesel resources on the Web
Do diesels have a future?
Vegetable oil yields and characteristics
Washing
Biodiesel and your vehicle
Food or fuel?
Straight vegetable oil as diesel fuel
Ethanol
Ethanol resources on the Web
Is ethanol energy-efficient?
|